If the last few years have taught us anything, a safe and secure pharmaceutical cold supply chain is of paramount importance – disruptions can directly put lives at risk. The pandemic highlighted the deficiency of current pharma supply chain operations: they operate reactively, not proactively. As innovation in drug research and development has increased the volume and variety of products sensitive to temperature deviations, coupled with unforeseen complexity in supply chains themselves, it’s never been more essential for companies in the pharma supply chain to have effective tools at their disposal to mitigate risk. Data, and more specifically, the combination of simulation (predictive) and operational (real-time) data, has the potential to make a seismic difference in building a reliable and effective pharmaceutical supply chain.
In 2019, the global export of pharmaceuticals was reported at $392.9 billion, and it has reached over $1 trillion since then. However, according to IQVIA Institute for Human Data Science, the biopharma industry loses approximately $35 billion annually as a result of failures in temperature-controlled logistics (data first shared in the 2019 Biopharma Cold Chain Logistics Survey Report). While vulnerabilities in the supply chain have always been present, the shortfalls have never been more consequential or pronounced than now. Events like the COVID-19 pandemic and the closure of airspace in response to the war in Ukraine, supply chains have needed to adapt faster than ever before.
Pervasive issues like spoilage, damage in transit and product theft not only affect the businesses’ return on investment but also have significant environmental and social consequences too. Unopened vial wastage is the industry’s biggest challenge, with the National Academies of Sciences, Engineering, and Medicine’s reporting that spoilage in the form of heat exposure or damaged packaging has resulted in almost $2.8 billion of medication being thrown away each year. During the height of the pandemic, supply chain theft peaked, with the Transport Asset Protection Association (TAPA) revealing almost €500,000 worth of goods were stolen from European, Middle Eastern and African supply chains every day, totalling €171 million in cargo thefts in just 18 months. Simply managing the ‘black box,’ is no longer a viable method for the industry; increased data-led visibility can have a dramatic impact on the industry, modernising it and striking a decisive blow against these perennial issues.
The supply chain’s visibility gap
Supply chain interruption is anticipated to a limited extent within the industry, with many implementing mitigation measures such as driver mandates and packaging materials that protect against temperature ranges. The ‘real life’ data or operational data (O-data) analyses what is actually happening during the shipment cycle. While supply chain companies are adept at collecting data to support this, the lack of visibility and access to data handling, assembling and execution of transport data has led to a ‘visibility gap,’ between what is understood to be happening and the actualities.
Simulation data (S-data), in the form of future risk assessments, temperature profiles, and packaging simulations solve the visibility gap between the actualities and possibilities of the future. Although supply chains analyse ‘S-data’, in the form of predicting potential fuel scarcities or expected turbulence, the depth and breadth of the analysis falls short, with industry players often unable to access the right data or produce a sufficient amount to make informed judgements.
Why is both S&O data necessary
Augmenting S-data with O-data helps those in the supply chain understand both what could happen and what is happening. Accessibility to the right data at the right time is key to improving transparency and planning more suitable transportation routes. Utilising sufficient real-time and simulation data at every stage of the supply chain can help prevent cross-contamination of product, product degradation, and even the infiltration of counterfeit products.
Access to real time data not only improves the return on investment as fewer products are wasted or lost, but also can usher in a transformational change in the industry , as the data collected can lead to better decision making that pushes the whole industry forward. Over-reliance on either operational or simulated data does not address the issue, which is why an interdependent approach is better, as it combines all the data in a purposeful way and creates truly actionable insights. For instance, it would be possible to know that turbulence was expected on a particular route (the O-data) but also that delays were historically a frequent occurrence at a particular airport, and that the cargo would in all likelihood spend more time than planned on the tarmac ( the S-data).
To build an agile, adaptable and resilient pharmaceutical supply chain, companies require access to comprehensive and accurate data that not only analyses what is happening, but what could happen with shipments. A true combination of S&O data doesn’t just improve transparency and visibility of cargo in transit, but also contributes to how companies are able to share these learnings with different departments across a business. This enables smarter and more profitable decision making based on data that unpacks their past, present and future, creating a more reliable and effective supply chain for us all.
About the Author
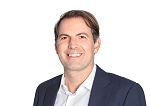
Nico Ros is a leading Swiss engineer and the co-founder and CTO of SkyCell. He is the mastermind behind SkyCell and its technology. Nico has always been curious about the functioning mechanisms behind the objects we use in our daily lives and has a passion for developing new technologies. Physics and maths are the subjects he finds the most intriguing and which found the basis of his career in engineering. Nico is also managing partner at ZPF, an engineering company in Basel. He has constructed some of the most expensive buildings in Switzerland in collaboration with architects like Herzog & DeMeuronand and has won prestigious architectural prizes. Nico’s key strength lies not only in his state-of-the-art engineering know-how but also in his ability to design from the ideal point and work that into the current technology and regulatory frameworks. He is also highly efficient at managing teams, leading highly complex, multimillion projects to success.
Sign up for the free insideAI News newsletter.
Join us on Twitter: https://twitter.com/InsideBigData1
Join us on LinkedIn: https://www.linkedin.com/company/insidebigdata/
Join us on Facebook: https://www.facebook.com/insideAI NewsNOW
Speak Your Mind